传统制造业的数字化转型浪潮下,企业常陷入这样的困境:投入百万升级生产线,却因研发环节的质量失控导致产品批量返工;组建了跨部门项目组,但FMEA报告和PPAP文件在流转中反复出错;明明引进了国际标准流程,但APQP五个阶段的执行总比竞争对手慢两拍……
当质量管理的复杂度突破人力极限,新一代高效智能APQP软件正成为破局关键。它不仅重构了产品研发的底层逻辑,更用数字化手段将质量风险拦截在生产线之外。
一、数据孤岛:跨部门协作如何破局?
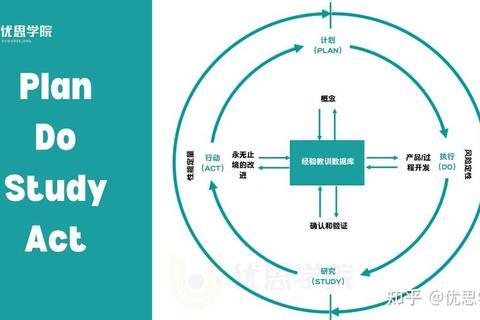
某汽车零部件企业曾因设计部门与生产部门数据不同步,导致新研发的涡轮增压器壳体在试制阶段出现26%的尺寸偏差。传统模式下,工程师需要手工整合来自12个系统的数据,仅DFMEA分析就耗费45人天。
引入高效智能APQP软件后(参考案例:全星APQP系统),该企业实现了APQP五大阶段数据的自动抓取与关联。通过集成FMEA、SPC、MSA等工具模块,设计参数变更会实时触发控制计划更新,工艺流程图与PFMEA的匹配度从68%提升至97%。在2024年某新能源车型的电机支架项目中,跨部门协作效率提升40%,问题追溯时间从8小时缩短至15分钟。
二、风险预测:质量问题能否提前拦截?
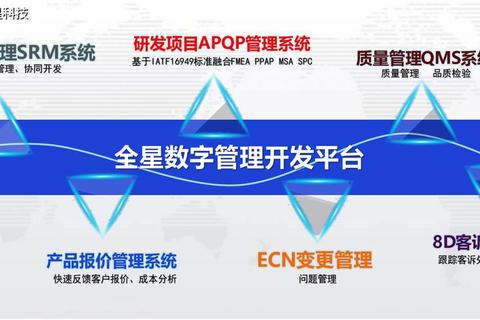
某半导体封装企业在芯片焊线工艺开发时,传统APQP流程直到试产阶段才发现金线弧度不合格。而采用智能APQP系统(参考案例:Opcenter APQP)的企业,早在设计验证阶段就通过历史数据比对,预警了4类潜在失效模式。
系统内置的AI模型会分析过往3000+项目的失效数据,当检测到新材料热膨胀系数异常时,自动推送7种改进方案。某连接器制造商应用该功能后,将过程能力指数CPK从1.0提升至1.67,客户投诉率下降62%。更关键的是,软件能自动生成符合IATF16949标准的PPAP文件包,将文档准备时间压缩80%。
三、动态优化:流程僵化难题如何破解?
家电行业某龙头企业曾因APQP流程僵化,新品类研发周期长达14个月。其症结在于传统阶段划分无法适应小批量定制化需求,每次工程变更都需要重新走完5大阶段审批。
部署智能APQP平台后(参考案例:某工业4.0解决方案),企业建立了动态里程碑机制。系统通过100+质量指标实时监控项目健康度,当SPC数据异常时自动触发纠正措施。在2024年智能马桶盖项目中,该企业通过软件推荐的敏捷开发路径,将过程验证周期从90天压缩至22天,同时将ECN(工程变更通知)响应速度提升3倍。
对于计划引入智能APQP系统的企业,建议分三步走:
1. 选择集成化平台:优先考虑能对接PLM、MES等现有系统的解决方案,避免形成新的数据孤岛(参考西门子Opcenter)
2. 关注自动化功能:重点考察AI生成FMEA、自动排程、智能预警等核心模块,实测文档生成准确率需达95%以上
3. 建立反馈机制:利用软件的数据沉淀功能,每季度分析APQP执行偏差率、问题关闭率等指标,持续优化质量基线
当高效智能APQP软件将风险管理从“事后灭火”转变为“事前预警”,当数据流转从“人工搬运”升级为“智能推送”,这场静悄悄的质量革命正在重塑制造业的竞争格局。那些率先完成数字化跃迁的企业,已然在客户满意度、市场响应速度、研发成本控制等方面建立起护城河。