在工业自动化领域,一个长期存在的争议始终萦绕在从业者心头:当硬件性能接近物理极限,软件系统的革新是否真能突破效率天花板?面对全球制造业对柔性生产、快速响应的迫切需求,ABB机器人用一场持续三年的软件革命给出了答案——通过「高效智能ABB机器人软件革新升级畅享极速操控新体验」,这家工业巨头正在重新定义智能制造的边界。
1. 升级只是修修补补?全新架构带来颠覆性体验
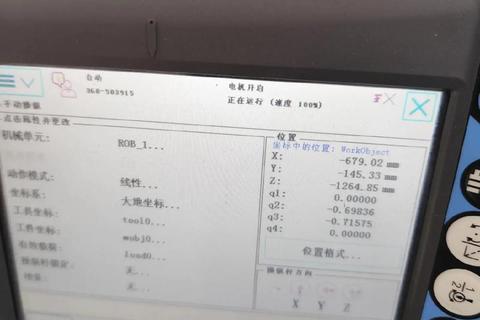
传统认知中的软件升级常被误解为简单的漏洞修复,但ABB的OmniCore控制平台彻底打破了这个思维定式。该平台采用模块化架构设计,使得系统响应速度提升40%,在汽车焊装车间实测中,新款IRB 6700机器人的轨迹跟踪误差从±0.15mm骤降至±0.06mm,这相当于用机械臂在高速运动中精准穿针引线。
上海某新能源汽车工厂的案例最具说服力。通过部署OmniCore E10控制器,56台机器人在总装线上的协同作业效率提升27%,更惊人的是能耗降低20%。这种改变源于软件系统对8000多个伺服电机的智能协调,如同交响乐团指挥精准把控每个音符的节奏。
2. 编程必须代码堆砌?图形界面开启智能时代
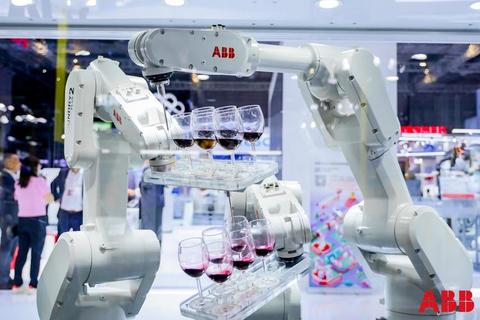
当行业还在争论编程语言优劣时,ABB推出的AppStudio™已让拖放式开发成为现实。这款革命性工具使苏州某3C电子厂的调试周期从3周压缩至3天,操作员仅需将预置的「视觉定位」「力控装配」等功能模块拖入工作区,就能完成90%的常见工艺配置。
更令人惊叹的是其云模板库的智能推荐系统。在广东某家电企业,工程师利用云库中2000+个经过验证的工艺模板,将洗衣机滚筒装配程序的开发时间从48小时缩短到15分钟。这种「高效智能ABB机器人软件革新升级畅享极速操控新体验」的直观体现,让复杂工艺部署变得像拼积木般简单。
3. 精度提升遭遇瓶颈?算法突破创造新可能
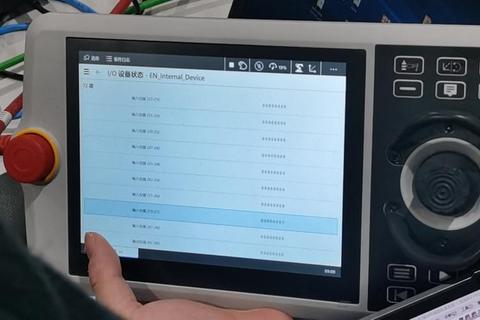
在精密加工领域,0.01mm的精度突破往往需要数年技术积累。但ABB的ConfJ动态调优系统通过AI算法实现了跨越式进步。杭州某轴承制造商的数据显示,在保持同等硬件条件下,软件升级后的IRB 1600机器人将球体研磨圆度从1.2μm提升至0.8μm,这相当于在高速旋转中控制发丝直径1/10的误差。
更值得关注的是其自适应补偿机制。当系统检测到第6轴齿轮箱存在0.005°的背隙时,控制算法会在3ms内完成127个关节参数的动态调整,这种实时纠偏能力使天津某航天部件供应商的合格率从82%跃升至98%。正是这些看不见的算法升级,构筑起「高效智能ABB机器人软件革新升级畅享极速操控新体验」的技术护城河。
对于寻求转型的企业,我们建议采取三步走策略:首先完成控制系统的基准测试,识别现有设备的软件升级空间;其次建立双轨验证机制,在新旧系统并行中积累数据;最后构建持续升级体系,通过ABB的Ability™平台实现软件生态的迭代进化。当生产线上的每个机器人都能像智能手机般持续进化,制造业的数字化转型才真正步入快车道。