一、传统经验公式为何被淘汰?
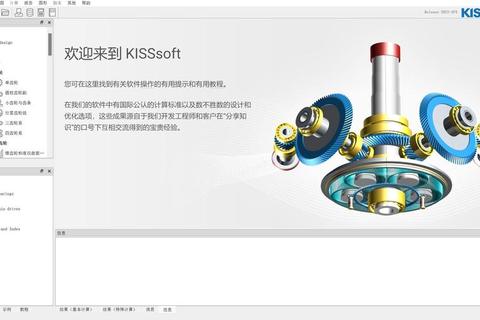
在齿轮设计领域,工程师们曾长期依赖经验公式和手册计算。例如某风电齿轮箱设计项目中,工程师按照传统方法计算齿轮模数为6,但实际测试发现齿面接触疲劳强度不足,导致设备在恶劣环境下出现早期失效。这种“设计-试制-测试-返工”的循环,让项目成本增加30%,周期延长4个月。
高效智能齿轮计算软件精准优化复杂传动设计的价值在此凸显。以KISSsoft为例,其基于ISO/AGMA标准的算法库可自动完成齿轮尺寸计算、强度校核和参数优化。某企业使用该软件后,将风电齿轮箱的齿面接触疲劳安全系数从1.2提升至1.8,同时齿轮体积减少15%。软件内置的案例库还能自动匹配相似工况数据,如针对高速重载齿轮的冲击载荷分析,可直接调用全球3000+工程案例进行对比验证。
二、多目标优化如何实现?
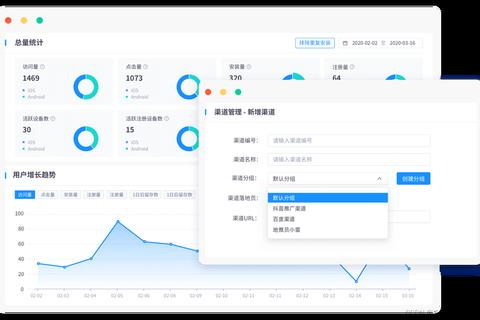
当某汽车企业设计混合动力变速箱时,需要在体积、传动效率、NVH性能之间取得平衡。传统方法只能进行单目标优化,而MATLAB优化工具箱通过建立多目标函数模型,将齿轮模数、齿宽系数、螺旋角等7个变量纳入计算,最终得到帕累托最优解集。数据显示,优化后的变速箱体积缩小22%,传动效率提升3.5%,噪音降低5dB(A)。
更值得关注的是软件对约束条件的智能处理。例如在搅拌机减速器设计中,系统自动识别出“螺旋角必须满足8°≤β≤15°”“齿宽系数需控制在0.8-1.2”等23项约束条件,并通过罚函数法将约束优化转化为无约束优化问题。最终方案使齿轮箱质量从133g降至111g,材料成本降低40%。
三、数字孪生技术如何赋能?
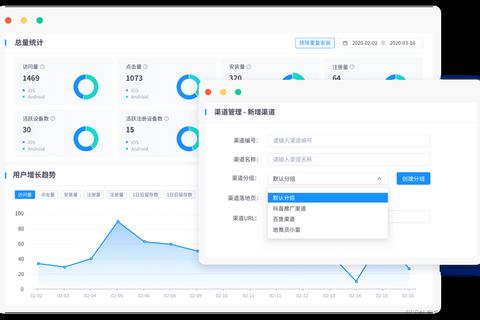
德国利勃海尔的高速干式滚齿机与西门子数控系统结合,展示了数字孪生的革命性价值。在加工机器人关节齿轮时,系统实时采集主轴振动(0.5μm精度)、切削温度(±1℃)等数据,通过数字孪生体预测刀具剩余寿命。实际应用表明,刀具更换间隔从500件提升至800件,废品率从2.3%降至0.7%。
国内某企业采用Altair CFD进行齿轮箱流固耦合仿真时,发现传统设计中的润滑油分布存在盲区。通过修改齿形修缘量和油道结构,使齿轮箱在-30℃低温启动时的磨损量减少60%,润滑油用量降低25%。
给工程师的实操建议:
1. 软件选型策略:优先选择支持ISO/AGMA双标准的工具(如KISSsoft),并验证其材料数据库是否包含40Cr、20CrMnTi等常用合金钢数据
2. 优化流程再造:建立“参数化建模→DOE实验设计→多目标优化→数字孪生验证”的四阶工作流,可缩短50%设计周期
3. 技术融合路径:将MATLAB算法模块与三维建模软件(如SolidWorks)集成,实现“计算-仿真-制造”数据贯通
4. 人才培养重点:加强工程师在智能算法(如遗传算法、粒子群优化)和跨学科知识(如热力学、流体力学)方面的能力建设
行业数据显示,采用高效智能齿轮计算软件精准优化复杂传动设计的企业,产品开发成本平均降低28%,故障率下降42%。这不仅是技术工具的升级,更是制造业向智能化转型的必经之路。